3D Printing
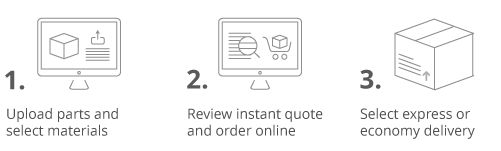
We offer two different 3D printing technologies
find out more about the technologies below
Process: Polyjet
PolyJet is a powerful 3D printing technology that produces smooth, accurate parts, prototypes and tooling.
With microscopic layer resolution and accuracy down to 0.1 mm, it can produce thin walls and complex geometries using the widest range of materials available with any technology.
Benefits of PolyJet:
- Create smooth, detailed prototypes that convey final-product aesthetics.
- Produce accurate molds, jigs, fixtures and other manufacturing tools.
- Achieve complex shapes, intricate details and delicate features.
- Incorporate the widest variety of colors and materials into a single model for unbeatable efficiency.
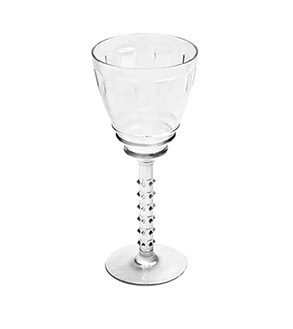
Material: Objet Vero Clear
VeroClear (RGD810) is a rigid, nearly colorless material featuring proven dimensional stability for
general purpose, fine-detail model building, 16 microns print layers and visual simulation of transparent thermoplastics, such as PMMA.
Please note: VeroClear requires polishing with wet and dry paper and lacquering to reach maximum clarity and has a frosted appearance by default.
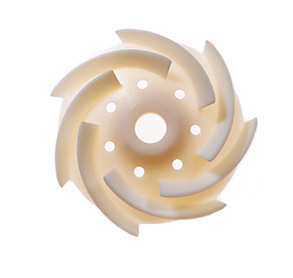
Material: Objet Vero White Plus
3D print accurate, prototypes to test fit, form and function. Vero White Plus combines excellent detail visualisation with strength, a key component in realistic prototypes.
Produce smooth, accurate prototypes, surgical models, moving and assembled parts, jigs, fixtures and manufacturing tooling. For multi-material versatility, blend with other photopolymers to vary hardness, flexibility or translucency.
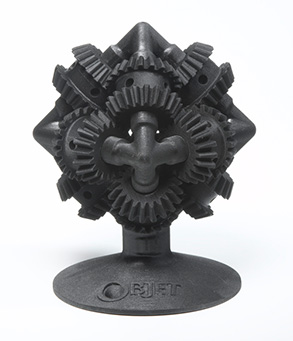
Material: Objet Vero Black Plus
3D print accurate, prototypes to test fit, form and function. Vero Black Plus combines excellent detail visualisation with strength, a key component in realistic prototypes.
Produce smooth, accurate prototypes, surgical models, moving and assembled parts, jigs, fixtures and manufacturing tooling. For multi-material versatility, blend with other photopolymers to vary hardness, flexibility or translucency.
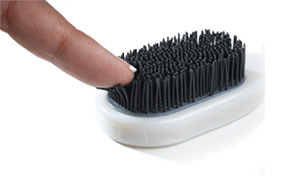
Material: Objet Agilus Black
Agilus30 is a PolyJet Photopolymer with superior tear-resistance, capable of withstanding repeated flexing and bending.
The ideal material for rapid prototyping and design validation, this rubber-like material simulates the look, feel and function of rubber-like products.
Agilus has a Shore A value of 30, blend it with other PolyJet photopolymers for different hardness, elongation and tear resistance levels.
Machine: Objet 260 Connex 3
Machine: Objet 260 Connex 3
Accuracy: +/- 0.1 mm
Build size: 255mm x 252mm x 200mm
Printing layer height: As fine as 14 microns
Build resolution: X-axis: 600 dpi; Y-axis: 600 dpi; Z-axis: 1600 dpi
Machine: Objet 30 Pro
Machine: Objet 30 Pro
Accuracy: +/- 0.1 mm
Build size: 300mm x 200mm x 150mm
Printing layer height: As fine as 14 microns
Build resolution: X-axis: 600 dpi; Y-axis: 600 dpi; Z-axis: 900 dpi
Design Guidelines: Objet
- Minimum wall thickness – 0.4mm (1mm for robust working material, walls less than 2mm may be translucent)
- Minimum printed thread size – M3
- Minimum hole diameter – 0.5mm
- Minimum text size and separation – 0.2mm
- Minimum emboss/engraving size – 0.2mm
Other tips:
- Hollow models to save weight/cost
- Fully enclosed regions should contain 1.5mm escape holes and blind holes should be through holes for effective support removal.
- Undersize tapping holes to minor diameter of screw or threaded insert, self-tapped holes will wear with continuous use.
- A 0.1mm gap gives an interference fit
- A 0.2mm gap gives a loose fit
- A 0.3mm gap gives a sliding fit
- Right angle internal walls are acceptable, but a 0.4mm radius is recommended for stress relief
- Areas beneath overhangs/undersides will be finished in matte, top surfaces and regions above overhangs can be matte or gloss.
- Connex Multimaterial Guidelines
- Multimaterial prints do not need offset between materials, but each material needs to be saved as separate stls
- A range of shore hardnesses and shades of grey and tints can be achieved
Process: FDM
FDM Technology works with specialized 3D printers and production-grade thermoplastics to build strong, durable and dimensionally stable parts with the best accuracy and repeatability of any 3D printing technology.
3D printers that run on FDM Technology build parts layer-by-layer from the bottom up by heating and extruding thermoplastic filaments.
3D printers powered by Stratasys’ industrial quality FDM technology feature layer heights as low as 0.2mm with an accuracy of approximately +/-0.1mm. ABS Plus thermoplastic models are resistant to high temperatures and abrasion; they are our tough, rugged and low cost option ideal for functional testing.
Material: ABS plus black
ABSplus is a production grade thermoplastic. Its strength, flexibility, machinability, and higher temperature resistance make it a preferred plastic for designers and engineers.
ABSplus is affordable, so designers and engineers can work iteratively, prototype often and test thoroughly.
But it’s also so durable that your concept models and prototypes perform much like the final product.
Machine: uPrint SE Plus
Machine: uPrint SE Plus
Accuracy: +/- 0.254 mm
Build size: 203mm x 203mm x 152mm
Printing layer height: As fine as 200 microns
Design Guidelines: FDM
- Minimum wall thickness – 0.8mm
- Minimum hole size – 0.5mm
- Minimum text size and separation – 0.2mm (orientation dependent, 1mm recommended)
- Minimum emboss/engraving size – 0.2mm (orientation dependent, 1mm recommended)
Other Tips:
- Hollow models to save weight/cost
- Solid or sparse infill options
- Fully enclosed regions should contain 1.5mm escape holes and blind holes should be through holes for effective support removal.
- Undersize tapping holes to lower diameter of screw or threaded insert, self-tapped holes will wear with continuous use
- A 0.2mm gap gives a tight fit
- A 0.3mm gap gives a sliding fit
- Right angle internal walls are acceptable, but 0.4mm radius is recommended for stress relief
- uPrint uses soluble support, so overhangs and bridges are printable